LafargeHolcim launches CO2-reducing cement business
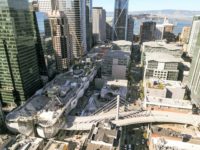

Brief:
- LafargeHolcim and Solidia Technologies announced this week that they have launched a new business in the U.S. that will supply customers with reduced CO2 cement to be used in the production of precast concrete. The first customer will be the Wrightstown, New Jersey, plant of EP Henry, a national concrete products supplier that participated in LafargeHolcim’s and Solidia’s pilot of the product.
- The product is the result of a six-year collaboration between LaFargeHolcim and Solidia and uses a special binder — produced at lower temperatures — and patented curing process that uses CO2 rather than water. By adding and absorbing CO2, Solidia Concrete reaches strength in less than 24 hours unlike precast concrete made with Portland cement, which takes 28 days to reach strength.
- Solidia reduces the overall carbon footprint in precast concrete by 70%. In addition, the new product reduces the cement plant’s carbon emissions by up to 40%.
Insight:
According to the Cicero Center for International Climate Research, cement manufacturing is No. 3 in carbon dioxide emissions behind fossil fuels and land-use change and the pace of production has increased by 30 times since the 1950s and by 40 times since 1990. Part of this growth is reflective of increased construction activity in China and other countries that have seen construction booms during the past few decades. U.S. Concrete says that one ton of cement production releases one ton of carbon dioxide into the atmosphere.
In response to concerns about climate change and cement production’s effect on the environment, innovations in concrete products have followed intensified imperatives and incentives to curb carbon in concrete production.
Last month, 1,400 U.S. mayors committed to working with low-carbon concrete in municipal infrastructure projects, adopting the resolution during the 87th Annual U.S. Conference of Mayors. During the event, officials pointed out that the material has already been used by several vendors in the country “without compromising the concrete’s quality, price or construction schedules.”
The cement industry has also moved toward the use of alternative raw materials. At U.S. Concrete, for example, this “EF Technology” includes using alternative cementitious materials, which result in lower greenhouse gas emissions. U.S. concrete says this change in the formula also makes for more durable and stronger concrete.
Alternative mix materials include fly ash and slag. Fly ash can replace up to half of the Portland cement usually used to produce concrete, and in addition to the environmental benefits of using less cement, fly can improve the workability and pumpability of concrete.
Slag, a byproduct of the smelting process, develops cementitious properties when mixed with water and provides more protection against alkali-silica and sulfate attacks. Using slag can also reduce the need for Portland Cement by up to 50%. By using a 50% slag mix, between 165 and 374 pounds of CO2 are saved per cubic yard of concrete, which translates to a reduction in greenhouse gas emissions by up to 46%.
This article was originally written by Kim Slowey and appeared here.
Comment (0)